Short Description
This study offers an in-depth exploration of the dynamic ecosystem of Perfom, a company that has established itself as an authority in the industry of perforated metal and related products. With a focus on its operational processes, challenges, and opportunities, the study outlines a roadmap for its digital transformation, highlighting key steps that will lead to even greater efficiency and productivity.
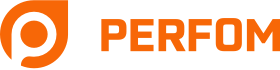
City: Požega
Website: https://perfom.rs/
Sector: Metal Processing Sector
Activity: Metal Manufacturing and Processing
Company Portrait
Perfom is not just a leading figure in the sector of manufacturing, processing and selling perforated metal and related products in Serbia and the region. This company inherits a rich history dating back to 1942 when it was founded as a family craft venture. Today, under the management of the fourth generation, it has evolved into the most technically sophisticated and expertly staffed factory in its field. Perfom now boasts a team of over 180 skilled employees and sophisticated operational processes. Their portfolio ranges from small to large product series, as well as custom-made prototypes according to clients’ specific requirements. Their clientele is not limited to large industrial players; on the contrary, they efficiently serve small entrepreneurs, craft workshops and individual clients.
Their products cater to a wide range of industrial sectors – from agriculture, mining and construction to shipbuilding, process industry and many others. With robust export operations, Perfom delivers products to global markets including, but not limited to, Germany, Austria, France.
Requirements
Perfom has long been proud of its application of modern equipment and CAD/CAM technologies, integrated with significant craftsmanship knowledge and experience. While the level of automation is already commendable, there are aspects that require further enhancement, especially in eliminating semi-automatic segments of production.
The company possesses a massive database stretching over more than two decades. This represents a “Big Data” potential and a fertile ground for implementing solutions based on artificial intelligence and machine learning. Annually, the company executes more than 2,500 projects, further emphasizing the value of this database.
Although investments have been made in ERP systems and significant initial steps towards digitalization have been taken, the data are fragmented and distributed between local infrastructure and various cloud services. Here, an opportunity for consolidation and better integration of information systems has been identified.
Within this critical area requiring urgent improvement, the focus is placed on the insufficient integration between the CAD/CAM platform and the business information system. The existing gap results in time losses for manual tool adjustments and slows down the overall efficiency of projects. There is significant potential for the application of machine learning which could automatically recognize and recommend optimal tool parameters, based on previous projects and experiences. This would enable more projects to be realized with the same, if not fewer, resources. and the Scandinavian countries.
One of the key aspects that set Perfom apart is their ability for rapid and quality tool development, thanks to their own tool shop and development department. This end-to-end approach, from conceptualization to production, ensures that all steps are optimized and tailored to client needs.
Finally, Perfom is committed to the continuous professional development of its employees. Internal training and certifications for working on CNC machines are a standard part of operations, while the application of the Kaizen method has been used for years as a tool for improving operational efficiency and productivity.
AI Solution
To address the previously mentioned challenges, the implementation project aims to enhance and integrate the existing digital resources and tools that Perfom already utilizes, specifically, its ERP system and CAD/CAM platform. With a database containing information on previously executed projects, the first step was to develop an intelligent solution for searching this database. By connecting with the ERP system, the solution now automatically generates components and materials directly from technical drawings, eliminating the need for manual labor, thereby significantly speeding up and optimizing business processes.
The implemented solution includes installing additional modules of the current CAD/CAM system vendor, which are also partly based on artificial intelligence algorithms. These modules will enable the automatic recognition of segments of projects that have been previously executed and may be relevant for new orders. In this way, the project will enable more efficient feasibility assessment and cost estimation for new projects.
The last, but not least, important component of this project is the implementation of advanced performance metrics that will allow operational teams to gain deeper insights into the status and progress of each project in real-time. Given that the company often manages multiple projects simultaneously, this functionality will be invaluable for efficient and effective resource and time management.
Measuring Success
The first of the project’s set goals, which pertained to the automatic definition of optimal product geometry and tool settings, was achieved with great success. Artificial intelligence now searches the database and identifies optimal solutions for each new project. This has led to a time-saving of over 15% in the tool setup processes, which used to be done manually.
The second goal, related to cloud data processing and collaborative designing, has also been fully realized. The development team now uses a unified cloud platform that supports all types of devices. This integration has eliminated all the errors that previously occurred due to data exchange, facilitating collaboration both within the team and with clients.
The third and final goal, increasing the productivity of employees in development and production, has also been achieved. Faster data exchange and reduced time needed for mutual communication and error correction have allowed for more projects to be processed in the same amount of time. Additionally, employees now have more time to focus on complex tasks, and thanks to detailed metrics, it is possible to track the performance of each individual project in real-time.
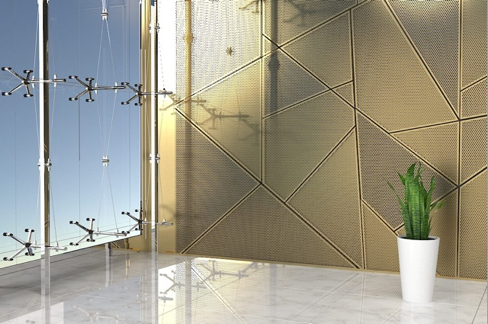
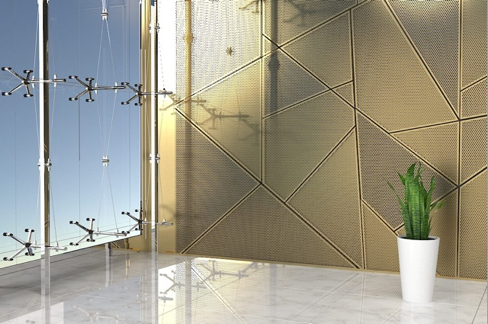
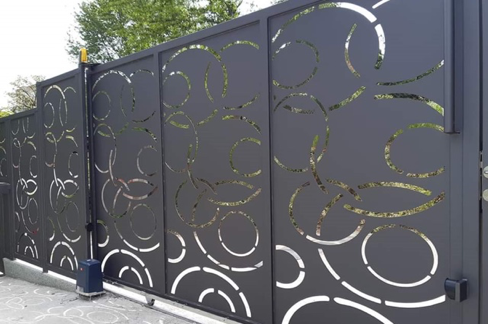
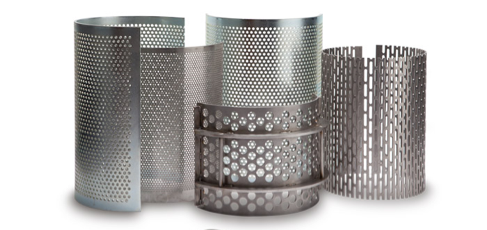
Concluding Considerations
Efficiency and time saving are critical factors in today’s business environment, and this is where artificial intelligence stands out by enabling quick and precise analysis of large volumes of data, essential for optimizing production processes.
In the context of a manufacturing plant, this is no small matter. AI can automatically adjust operations to reduce the resources and energy required for production. Essentially, it is a system that “learns” and improves over time, bringing real savings and increasing productivity.
While AI offers many possibilities, it is important to note that it is merely a tool. Technology cannot replace human expertise and intuition; it is there to enhance it. Therefore, it is crucial that AI is implemented and used responsibly.